Surface Mount Technologies (SMT)
Why should electronics manufacturers adopt surface mount technology (SMT)?
- lower product costs
- integrate higher component density
- improve product performance

Converting legacy through-hole designs to SMT Quickly pays for itself.
Advantages of SMT
In the early days of electronics, boards were assembled using the through-hole method.
This meant drilling holes to accept the long leads on every component. These leads were then soldered to the board.
In the 1980s the industry began switching to surface mount technology. There were three drivers for this:
- Lower cost. Drilling is eliminated, components can be placed and soldered automatically, and it's possible to use both sides of the board.
- Smaller components. Surface mount devices (SMDs) whether active or passive, are more compact than through-hole. This means boards can be smaller and lighter — or more components can be placed on a board.
- Better performance. Eliminating component leads means less inductance and resistance. As a result, SMT boards usually perform better and tend to be more reliable.
SMT Challenges
In the early days of electronics, boards were assembled using the through-hole method.
This meant drilling holes to accept the long leads on every component. These leads were then soldered to the board.
In the 1980s the industry began switching to surface mount technology. There were three drivers for this:
- Lower cost. Drilling is eliminated, components can be placed and soldered automatically, and it's possible to use both sides of the board.
- Smaller components. Surface mount devices (SMDs) whether active or passive, are more compact than through-hole. This means boards can be smaller and lighter — or more components can be placed on a board.
- Better performance. Eliminating component leads means less inductance and resistance. As a result, SMT boards usually perform better and tend to be more reliable.
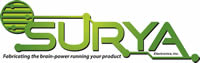
What Surya Can Do for YOU
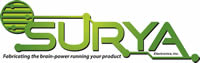
Converting an older through-hole printed circuit board assembly to SMT needs electrical engineering expertise coupled with an intimate understanding of surface mount manufacturing processes.
Surya was the first company in Illinois to own and operate a complete SMT line back in 1984. Surya subcontracted SMT to many of its competitors who did not have this capability. To this day Surya remains the #1 source for SMT production.
With four complete SMT lines capable of high volume or low volume high mix, Surya can handle any size demand and keep up with a continual production procurement cycle.
Supporting our SMT manufacturing processes, we also offer extensive inspection and testing. Automated Optical Inspection (AOI) lets us inspect finished boards quickly while our microscope and X-ray services provide additional assurance that they will be defect-free.
Design Review
Professional engineers need boards quickly that perform optimally. Whether you specialize in medical, industrial or consumer devices, we know you don’t have time for errors. That’s why our human inspectors comb through your PCB design to find every little glitch BEFORE it grows into a big malfunction.
The goal is to produce a board formula that’s more reliable and much closer to market-ready.
Process
State-of-the-art printed circuit boards don’t just happen by chance. Don’t let our traditional red brick exterior fool you; we’re continually optimizing workflows and training for new technologies. When a Surya specialist navigates your bare board production process, expect your board to be manufactured
faster and perform better.
Cost Reduction
With over 30 years of experience, we know every avenue and can leverage our connections to attain the lowest possible pricing. With all that experience we can’t help but produce the most efficient, most cost-effective PCBAs at the lowest possible price.
Quality
We don’t like to brag, but numbers don’t lie: Surya Electronics has a 97% first-build success rate and and Surya is know for its accurate and on-time delivery. That’s guaranteed — because for Surya, quality doesn’t happen by accident, it’s built into our processes.
Our Capabilities
Learn more by watching our video or clicking the links below.